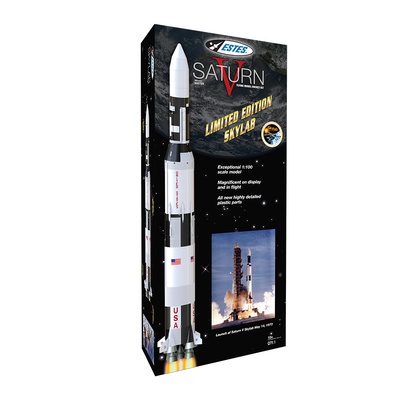
Product Description
DESCRIPTION

(Formerly Skill Level 5)
Between 1967 and 1973, NASA successfully launched 13 Saturn V rockets – two were unmanned test flights, nine carried astronauts to the moon or Earth orbit, and one, the last Saturn V, had a mission unlike any other. This was the launch of the first American space station, an enormous orbital habitat called Skylab.
Apollo was not meant to be a singular achievement. After a series of moon landings, NASA expected to transition to the Apollo Applications Program (AAP) which would have used the hardware developed for the moon missions to support expanded space exploration activities. AAP would have deployed Lunar Module cargo carriers and astronaut “taxis,” lunar surface habitats, and orbital space stations. But NASA’s funding was diminishing and by the time of Armstrong’s “Giant Leap” the public and Congress had lost the drive to keep space exploration a priority. Apollos 18, 19 and 20 were canceled even though much of the hardware had already been paid for and built.
In an attempt to salvage some part of AAP and utilize the hardware on hand, a single Earth orbital space station – Skylab – was proposed. The space station was constructed from a modified S-IVB stage and on May 14, 1973, was lifted to orbit by the Saturn V’s powerful first and second stages. Compared to the Apollo Command Module, the interior volume of the Skylab orbital workshop was vast, with room for a crew of three to live and work in relative comfort. Eventually, three separate crews called Skylab home for successively longer missions, culminating in an 84 day stay between November 1973 and February 1974. Although there were plans to keep Skylab aloft indefinitely for future crews, unexpected orbital decay brought the massive space station down in 1979, scattering its parts across Western Australia.
The Estes Saturn V Skylab is an accurate 1:100 scale reproduction of this historic rocket and its space station payload. Vacuum formed tube wraps and fin fairings add a textured realism to this model’s surface. Injection molded fins are both durable and detailed – a fin alignment guide is included for precise placement. The detailed water-slide decals accurately represent the markings of this historic mission. Before flight, remove the realistic engine nozzle assembly and prep for launch. The Estes Saturn V Skylab can reach up to 400 feet on an Estes F15-4 engine. At ejection, the rocket separates into two sections for recovery – the Saturn V first and second stages return together under dual 24-inch parachutes, while the Skylab upper section sports its own 18-inch canopy. With impressive E-engine launches and multi-segment, multi-parachute recoveries, the Estes Saturn V Skylab will stand out in any model rocket fleet!
ADDITIONAL INFORMATION
Recommended Engines |
E16-4, F15-4 |
---|---|
Projected Max Altitude |
400 ft. (122 m) |
Recovery System |
1x 18 in. (45.7 cm) Parachute |
Diameter |
3.94 in. (100 mm) |
Length |
41.25 in. (104.8 cm) |
Estimated Weight |
17 oz. (481.9 g) |
Estimated Assembly Time |
12 Hours (painting and glue drying time not included) |
Fin Materials |
Plastic |
Decal Type |
Waterslide |
Launch System |
Porta-Pad E and E Launch Controller |
Launch Rod Size |
1/4" |
Customer Reviews
-
Balanset-1A: Make the right choice for your business
static balancing Static Balancing: Understanding the Basics Static balancing is a crucial concept in the field of rotor mechanics, particularly for ensuring the smooth operation of various machinery. When discussing static balancing, it is essential to differentiate it from dynamic balancing, as each serves distinct purposes and applications. This article will delve into the principles of static balancing, its processes, and its significance in mechanical systems. What is Static Balancing? Static balancing refers to the state where the center of gravity of a rotor coincides with its axis of rotation. When a rotor is statically unbalanced, its center of gravity is offset from this axis, leading to a phenomenon where the heavier part of the rotor tends to rotate downward under the influence of gravity when the rotor is stationary. The goal of static balancing is to adjust the mass distribution around the rotor to eliminate this imbalance. Static Balance vs. Dynamic Balance It is fundamental to understand the difference between static and dynamic balance: Static Balance: Occurs when the rotor is stationary. It addresses the mass distribution in a single plane, ensuring that the heavy point is directly downward when the rotor is at rest. Dynamic Balance: Occurs during rotation and involves unbalance in two or more planes. It is more complex and requires understanding how forces within the rotor interact, often leading to vibrations due to two different mass displacements. Importance of Static Balancing Static balancing is particularly significant for rotors that operate at low speeds or are simply stationary at particular moments during their operation. Proper static balancing ensures minimal vibrations and wear on the machinery, thereby improving operational efficiency and extending the lifespan of components. Process of Static Balancing 1. Initial Assessment The first step in static balancing involves an initial assessment of the rotor to identify any imbalances. This assessment typically requires measuring vibrations and observing how the rotor behaves under various conditions. 2. Adding or Removing Mass To achieve a static balance, specific weights may need to be added or removed from the rotor. This process will take place at precise points along the rotor, focused on aligning the center of gravity with the axis. 3. Verification Once weights have been adjusted, the rotor is tested once more to verify that the initial unbalance has been corrected. This verification process involves running the rotor and re-measuring vibrations. Applications of Static Balancing Static balancing is widely applied across various industries, particularly where rotors are involved. Below are a few examples: Fans: Fans require static balancing to ensure that they operate smoothly without generating excess vibrations. Crushers: In crushing machinery, static balancing can prevent structural failures and improve overall efficiency. Augers: Used in agricultural and industrial settings, augers benefit from static balancing to enhance performance and reduce wear. Centifuges: Static balancing is critical to ensure that centrifuges function correctly and effectively separate materials. Static Balancing Techniques There are varied techniques for achieving static balancing: Trial Weights: Using trial weights involves temporary adjustments that help gauge the required corrections before making permanent changes. Instrumentation: Utilizing specialized instruments allows for accurate measurement of vibrations, aiding in determining the location and amount of mass needed for balancing. Conclusion In summary, static balancing is a vital process for ensuring optimal rotor performance by aligning the center of gravity with its axis of rotation. Understanding static balancing, its applications, and the method used to achieve it can help prevent complications related to mechanical vibrations, inefficiencies, and premature wear in machinery. Proper execution of static balancing can lead to smoother operations and improved longevity of equipment across numerous industrial applications. By ensuring that rotors are statically balanced, industries can benefit from enhanced operational productivity and reduced maintenance costs, making it an essential practice in the realm of mechanical engineering.
Reviewed by JeremycausH on Nov. 21, 2024, 9:44 p.m. | Permalink
This review has no votes.